|
 |
Revised: January 2007
Issued: June 1, 1987
Disclaimer
The documents in HTML format that are provided on this Web site have been
prepared for use as a ready reference and do not have legal force or effect.
A Portable Document Format (PDF) version is provided for the purposes of
interpretation and application. The PDF version may be viewed using version
3.0 or higher of the Adobe® Acrobat Reader, which may be downloaded
free of charge by visiting the Adobe®
Web site. |
TABLE OF CONTENTS
LIST OF FIGURES
LIST OF REFERENCED DOCUMENTS
Drawing Package NHTSA SAS–100–1000
Society of Automotive Engineers Recommended Practice J211, Instrumentation
for Impact Tests (October 1988)
American Society for Testing and Materials:
Standard Practice for Determination of Weight and Shape Changes of
Plastics Under Accelerated Service Conditions, Designation No. D 756-93
Standard Practice for Operating Light-Exposure Apparatus (Carbon-Arc
Type) With and Without Water for Exposure of Nonmetallic Materials,
Designation No. G 23-96
Standard Practice for Operating Salt Spray (Fog) Testing Apparatus,
Designation No. B 117-95
Standard Practices for Force Verification of Testing Machines,
Designation No. E 4-96
Standard Specification for Flexible Cellular Materials–Sponge
or Expanded Rubber, Designation No. D 1056-91
Standard Specification for Flexible Cellular Materials–Vinyl
Chloride Polymers and Copolymers (Open-Cell Foam), Designation No.
D 1565-81 (Reapproved 1990)
Standard Test Methods for Flexible Cellular Materials–Slab,
Bonded, and Molded Urethane Foams, Designation No. D 3574-95
American Association of Textile Chemists and Colorists:
Evaluation Procedure 1, Gray Scale for Color Change
Test Method 30-1993, Antifungal Activity, Assessment on Textile Materials:
Mildew and Rot Resistance of Textile Materials
Test Method 107-1991, Colorfastness to Water
Test Method 8-1996, Colorfastness to Crocking: AATCC Crockmeter Method
|

2.
| Test Devices to be Used for the Dynamic Test for Production
Restraint Systems and the Buckle Release Tests
2.1 The seat to be used for
the dynamic test prescribed in this test method is the standard seat assembly,
as described in Drawing Package NHTSA SAS-100-1000 and shown in Figure 1(a), which indicates the location
of the seat belt anchorage points, and Figure
1(b), which indicates the location of the lower universal anchorage
system, mounted on a dynamic test platform so that the Seat Orientation
Reference Line (SORL) is parallel to the direction of travel of the test
platform and so that movement between the base of the assembly and the
platform is prevented.
2.2 The test platform must be instrumented with an accelerometer
that is linked to a data processing system, and the accelerometer-sensitive
axis must be parallel to the direction of travel of the test platform.
The data must be filtered with a Class 60 filter, as specified in the
Society of Automotive Engineers Recommended Practice J211, Instrumentation
for Impact Tests (October 1988).
|
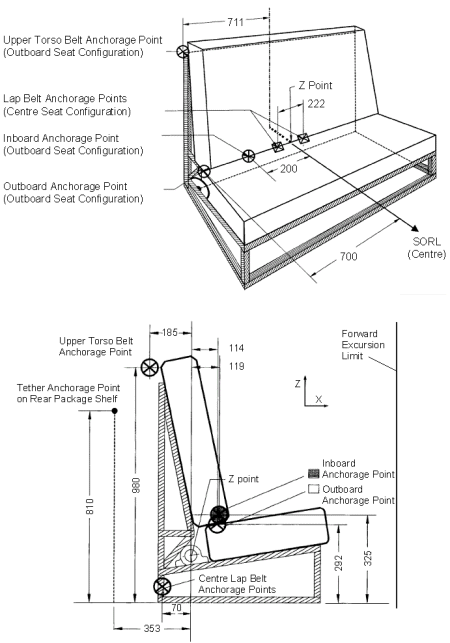
| Notes:
1. Dimensions are in mm, except where otherwise indicated.
2. Drawings are not to scale.
3. Lap belt anchorage points are symmetrically located with respect to
the centre SORL.
4. Maximum distance from the seat bight to the end of the buckle is 175
mm.
5. Outboard anchorage point is located 700 mm from the centre SORL.
6. Anchorage point on the rear package shelf is located on the vertical
longitudinal plane containing the centre SORL.
|
Figure 1(a) Three-dimensional Schematic View
and Side View of the Standard Seat Assembly Indicating the Location of the Seat
Belt Anchorage Points

| Notes:
1. Dimensions are in mm, except where otherwise indicated.
2. Drawings are not to scale.
3. Lower universal anchorage system bars are 6 mm in diameter and 25 mm
in length.
4. Transverse horizontal distance between the centre of the bars and the
vertical plane containing the SORL at the centre of the seat assembly
is 140 mm.
5. Anchorage point on the rear package shelf is located on the vertical
longitudinal plane containing the centre SORL.
6. Head excursion limit is 720 mm.
7. Lower universal anchorage system bars are located 102 mm forward of
Z Point and 323 mm above the floor.
|
Figure 1(b) Three-dimensional
Schematic View and Side View of the Standard Seat Assembly Indicating the Location
of the Lower Universal Anchorage System
| 2.3 Type 1 or Type 2 seat belt assemblies that
meet the requirements of section
209 of the Motor Vehicle Safety Regulations and whose webbing
is not more than 50 mm wide must be attached, without the use of retractors
or reels of any kind, to the seat belt anchorage points provided on the
standard seat assembly.
2.4 The anthropomorphic test device (ATD)
to be used in the dynamic test and the buckle release tests must be
of the appropriate height and mass for the system being tested, and
it must conform to the dimensions and mass given in Figure
2 for that type of ATD. The ATD must be clothed in form-fitting
cotton stretch underwear with short sleeves and mid-calf length pants.
It must also wear sneakers with rubber soles and cotton or nylon uppers
of the appropriate size.
|

Symbol and Description
|
3-Year-Old Child ATD
|
6-Year-Old Child ATD
|
5th Percentile
Adult Female
ATD
|
50th Percentile
Adult Male
ATD
|
Standing height
| 973
| 1212
| 1499
| 1735
|
Mass in kg
| 15.1
| 21.5
| 46.3
| 74.7
|
I: Shoulder-elbow length
| 173
| 234
| 318
| 358
|
J: Elbow rest height
| 158
| 183
| 203
| 241
|
L: Popliteal height
| -
| 325
| 373
| 439
|
M: Knee height (sitting)
| 264
| 368
| 447
| 544
|
N: Buttock-popliteal length
| -
| 345
| 432
| 495
|
O: Chest depth
| 127
| 163
| 191
| 236
|
P: Buttock-knee height
| 325
| 406
| 531
| 592
|
Q: Thigh clearance
| 86
| 112
| 117
| 145
|
R: Elbow-fingertip length
| 254
| 320
| 401
| 475
|
S: Foot length
| 147
| 175
| 216
| 267
|
T: Head length
| 170
| 178
| 173
| 196
|
U: Sitting height (erect)
| 569
| 645
| 785
| 907
|
V: Shoulder breadth
| 236
| 264
| 381
| 455
|
W: Foot breadth
| 58
| 66
| 84
| 97
|
X: Head circumference
| 508
| 526
| 518
| 572
|
Y: Chest circumference
| 511
| 597
| 757
| 958
|
Z: Waist circumference (sitting)
| -
| 528
| 599
| 838
|
AA: Head breadth (sitting)
| 137
| 150
| 137
| 154
|
BB: Hip breadth (sitting)
| 180
| 213
| 325
| 384
|
CC: Hip circumference (sitting)
| -
| 607
| 925
| 1067
|
Note: The dimensions are in mm, unless otherwise specified.
Figure 2 Physical Dimensions
and Masses of the ATDs
3.
| Dynamic Tests for Production Restraint Systems
A first dynamic test is to be conducted
in accordance with the procedure set out in subsections 3.4
and 3.5 using a new production restraint system
for disabled persons that is attached to the standard seat assembly as
shown in Figure 1(a) by the seat belt assembly
and a tether strap, if one is provided with the system.
If the restraint system is equipped with a lower connector system, a
second dynamic test is to be conducted in accordance with the procedure
set out in subsections 3.6 and 3.7 using a
new production restraint system for disabled persons that is attached
to the standard seat assembly as shown in Figure 1(b) by the lower universal anchorage
system and a tether strap, if one is provided with the system.
3.1 Test Acceleration
The dynamic tests simulate a frontal impact at 48 km/hr. At all points
in time until 48 milliseconds after the start of the pulse, the acceleration
of the test platform must be above that indicated by the line shown in
Figure 3 and such that the total change of velocity
is at least 48 km/h.
|

Figure 3 Test Platform Acceleration Graph
| 3.2 Test Conditions
For the dynamic tests, the ambient temperature must be from 19°C
to 26°C and the relative humidity from 10% to 70%.
3.3 Pre-Test Buckle Release Force Measurement
If the belts of the restraint system are equipped with buckles, the
release force of each buckle is to be measured in the following manner
before commencing the dynamic tests.
3.3.1 Place the buckle assembly on a hard, level surface.
3.3.2 Apply a pullout force of 9 N to the buckle assembly in
a direction that will produce maximum releasing effect, in the case of
(a) A push-button-actuated buckle, on the centreline of the push-button
opening of the buckle, or
(b) A lever-actuated buckle, at least 3 mm from the edge of the buckle
lever or finger tab.
3.3.3 Measure the force required to release
the buckle and determine its conformance to the requirements of Schedule
6 to the RSSRs.
3.4 Positioning of the ATD and Installation
of the Production Restraint System for the Dynamic Test Using the Seat
Belt Assembly
3.4.1 In accordance with the manufacturer's instructions, place
a new production restraint system at the centre seating position of the
standard seat assembly and position each movable surface. If the restraint
system is installed by passing the motor vehicle seat belt over the system
and under the seated ATD, attach the seat belt to the restraint system,
but do not tighten it.
3.4.2 Place the ATD specified in subsection 2.4
in the restraint system and position it according to the manufacturer's
instructions and as follows:
(a) Holding the torso upright until it contacts the seat back of the
system, seat the ATD in the restraint system so that the mid-sagittal
plane of its head is coincident with the SORL of the standard seating
assembly.
(b) Lift the arms of the ATD as far upward as possible. Extend the
legs of the ATD as far forward horizontally as possible, with its feet
perpendicular to the centreline of the lower legs.
(c) Using a flat square surface with an area of 2 580 mm², apply
a force of 180 N perpendicular to the plane of the back of the standard
seat assembly, first against the crotch of the ATD and then against
the mid-sagittal plane of its thorax.
(d) Attach all the appropriate restraint system belts and harnesses
and tighten them as specified in subsection 3.4.3.
(e) Rotate each limb of the ATD downward in a plane parallel to its
mid-sagittal plane until the limb touches a surface of the restraint
system or the standard seat assembly. Position the limbs so that they
will not inhibit the movement of the torso or head during the test.
3.4.3 If shoulder and pelvic belts are provided
that directly restrain the ATD, they must be adjusted by tightening the
belts until a 9-N force applied using a webbing tension pull device (as
illustrated in Figure 4) to the webbing at the
top of each shoulder and to the pelvic webbing 50 mm on either side of
the mid-sagittal plane of the torso pulls the webbing a distance of 7
mm away from the ATD.
|

Figure 4 Webbing Tension Pull Device
| 3.4.4 In accordance with the manufacturer's instructions,
attach the production restraint system, if it is not already installed,
to the standard seat assembly using the motor vehicle seat belt and attach
the tether strap, if one has been provided. Tighten the seat belt and
tether strap to a tension, as measured by a force gauge used on the webbing,
of
(a) until August 31, 2002, not less than 31 N and not more than 49
N or, at the option of the manufacturer, not less than 53.5 N and not
more that 67 N; and
(b) on or after September 1, 2002, not less than 53.5 N and not more
than 67 N.
3.5 Test Procedure
3.5.1 Accelerate the test platform in accordance with the requirements
of subsection 3.1.
3.5.2 Measure the excursion of the ATD and determine the conformance
of the restraint system to the requirements of section 12 of Schedule
6 to the RSSRs.
3.6 Positioning of the ATD and Installation
of the Production Restraint System for the Dynamic Test Using the Lower
Universal Anchorage System
3.6.1 In accordance with the manufacturer's instructions, place
a new production restraint system at the centre seating position of the
standard seat assembly and position each movable surface. As specified
in subsection 3.6.4 and in accordance with the manufacturer's
instructions, attach the lower connectors of the restraint system to the
lower universal anchorage system and attach the tether strap, if one has
been provided, to the standard seat assembly, but do not tighten it.
3.6.2 Place the ATD specified in subsection 2.4
in the restraint system and position it according to the manufacturer's
instructions and as follows:
(a) Holding the torso upright until it contacts the seat back of the
system, seat the ATD in the restraint system so that the mid-sagittal
plane of its head is coincident with the SORL of the standard seating
assembly.
(b) Lift the arms of the ATD as far upward as possible. Extend the
legs of the ATD as far forward horizontally as possible, with its feet
perpendicular to the centreline of the lower legs.
(c) Using a flat square surface with an area of 2 580 mm², apply
a force of 180 N perpendicular to the plane of the back of the standard
seat assembly, first against the crotch of the ATD and then against
the mid-sagittal plane of its thorax.
(d) Attach all the appropriate belts and harnesses on the restraint
system and tighten them as specified in subsection 3.6.3.
(e) Rotate each limb of the ATD downward in a plane parallel to its
mid-sagittal plane until the limb touches a surface of the restraint
system or the standard seat assembly. Position the limbs so that they
will not inhibit the movement of the torso or head during the test.
3.6.3 If shoulder and pelvic belts are provided
that directly restrain the ATD, they must be adjusted by tightening the
belts until a 9-N force applied using a webbing tension pull device (as
illustrated in figure 4) to the webbing at the
top of each shoulder and to the pelvic webbing 50 mm on either side of
the mid-sagittal plane of the torso pulls the webbing a distance of 7
mm away from the ATD.
3.6.4 (a) Adjust rigid lower connectors in
accordance with the manufacturer's instructions;
(b) If a tether strap has been provided, tighten it to a tension of
not less than 53.5 N and not more than 67 N, as measured by a force
gauge used on the webbing.
3.7 Test Procedure
3.7.1 Accelerate the test platform in accordance with the requirements
of subsection 3.1.
3.7.2 Measure the excursion of the ATD and determine the conformance
of the restraint system to the requirements of paragraph
12(1)(d) of Schedule 6 to the RSSRs.
|
4.
| Buckle Release Test Procedure for Production Restraint
Systems
4.1 The release force of each buckle is
to be tested with the ATD specified in subsection 2.4
of this test method retained in the restraint system.
4.2 The buckle release force is to be tested as follows:
(a) Tie a self-adjusting sling to the wrists and ankles of the ATD,
as illustrated in Figure 5.
(b) While applying a pullout force of 9 N to the buckle assembly in
a direction that will produce maximum releasing effect, pull the sling
horizontally and parallel to the SORL of the standard seat assembly
with a force of 200 N.
Note: If the restraint system is equipped with a T-shield, a force
equivalent to its mass must be added to the pullout force. Any shield,
if present, may be adjusted to facilitate application of the pullout
force, provided that the harness tension is not significantly affected.
(c) In order to determine the buckle's conformance to the requirements
of Schedule
6 to the RSSRs, apply the specified force in a direction that will
produce maximum releasing effect, in the case of
(i) A push-button-actuated buckle, on the centreline of the push-button
opening, or
(ii) A lever-actuated buckle, at least 3 mm from the edge of the buckle lever
or finger tab.
(d) If the force required to release the buckle exceeds the requirements
of Schedule
6 to the RSSRs, release the harness tension and apply a force of
22 to 44 N to the lowest accessible part of the tongue 2 to 4 times
in each of four directions at 90-degree angles to each other.
(e) Repeat paragraphs (b) and (c) above while applying a pullout force
on the buckle assembly of 22 N, re-orienting the direction of the sling
pull force if necessary so that the arms of the ATD do not load the
shield.
(f) If the buckle does not release at the force specified in Schedule
6 to the RSSRs, repeat paragraphs (b) and (c) once again using a
pullout force of 44 N.
|

Figure 5 Self-Adjusting Sling for the Buckle Release Test
5.
| Buckle Release Test Procedure for Custom-Made Restraint
Systems
5.1 The
seat belt assembly must be subject to a force on the components of the
buckle of either:
(a) 333 N when the maximum recommended mass of the occupant is 22
kg or more, or
(b) 200 N when the maximum recommended mass of the occupant is less
than 22 kg.
5.2 The buckle release force must be applied in a manner and
direction typical of those encountered in use.
5.3 For push-button-actuated buckles, the force must be applied
on the centreline of the push-button opening in a direction that produces
maximum releasing effect. For lever-actuated buckles, the force must be
applied at least 3 mm from the edge of the buckle lever or finger tab
in a direction that produces maximum releasing effect.
5.4 For push-button-actuated buckles, the area
to which the release force is applied must be determined to the nearest
32 mm². For lever-actuated buckles, a cylinder 10 mm in diameter
and 38 mm in length must be inserted into the actuation portion of the
buckle in order to determine its conformance with the requirements of
subsection 5.1. Buckles with other release actuation
mechanisms must be examined to ensure that the fingers can be inserted.
5.5 The belt buckle must be subjected to a
compressive force of 1 780 N applied anywhere on a test line that coincides
with the centreline of the belt when it is extended through the buckle
or on any line that extends over the centre of the release mechanism.
The latter line must intersect with the extended centreline of the belt
at an angle of 60°. The load must be applied by using a curved cylindrical
bar having a cross-sectional diameter of 19 mm and a radius of curvature
of 150 mm, placed with its longitudinal centreline along the test line
and its centre directly above the point on the buckle to which the load
will be applied. The buckle must be latched, and a tensile force of 333
N must be applied to the connected webbing during the application of the
compressive force.
|
6.
| Energy Absorbing Material Test Procedure for All Restraint
Systems
6.1 Prepare and test specimens
of energy absorbing material in accordance with the applicable 25% compression-deflection
test specified in one of the following American Society for Testing and
Materials (ASTM) Standards:
- Standard Specification for Flexible Cellular Materials–Sponge
or Expanded Rubber, Designation No. D 1056-91;
- Standard Specification for Flexible Cellular Materials–Vinyl
Chloride Polymers and Copolymers (Open-Cell Foam), Designation No.
D 1565-81 (Reapproved 1990); or
- Standard Test Methods for Flexible Cellular Materials–Slab,
Bonded, and Molded Urethane Foams, Designation No. D 3574-95.
6.2 Determine the conformance of the test specimens to the requirements
of section
5 of Schedule 6 to the RSSRs.
|
7.
| Flammability Test Procedure for All Restraint Systems
7.1
Test Devices
7.1.1 Flammability Test Cabinet: In order to protect the
test specimens from drafts, the flammability test must be conducted in
a cabinet constructed in accordance with the following specifications
and as illustrated in Figure 6. The flammability
test cabinet must be constructed of metal and must have:
(a) an interior length of 381 mm, a depth of 203 mm, and
a height of 356 mm;
(b) a glass observation window in the front;
(c) a closeable opening to permit the insertion of a specimen holder;
(d) a hole to accommodate tubing for a bunsen burner; and
(e) for ventilation, a clearance space of 13 mm around the top of
the cabinet, ten holes 19 mm in diameter in the base of the cabinet,
and legs that elevate the cabinet by 10 mm.
7.1.2 Specimen holder: The test specimen must be mounted
between two U-shaped frames of metal stock 25 mm wide and 10 mm
high. The dimensions of the interior U of each frame must be 51 mm
by 330 mm.
|

Figure 6 Flammability Test Cabinet
| 7.1.3 A specimen that softens
and bends at the flaming end in a manner that causes erratic burning must
be kept horizontal by using either of the following inserted along the length
of the bottom frame under the specimen:
(a) supports consisting of thin, heat-resistant wires distributed
at 25-mm intervals or
(b) an additional U-shaped frame that is wider than the specimen holder
with heat-resistant wires 254 µm in diameter, distributed
at 25-mm intervals.
7.2 Test Conditions
7.2.1 Prior to testing, each specimen must be conditioned for
24 hours at a temperature of 21°C and a relative humidity of 50%.
The test must be conducted under these ambient conditions.
7.2.2 A bunsen burner with an interior diameter
of 10 mm must be used for the test. With the air inlet to the burner
closed and the burner vertical, the gas adjusting valve must be set to
provide a flame 38 mm in height. The flame temperature must be equivalent
to that of natural gas.
7.2.3 The test specimen must be rectangular in shape and 102 mm
wide by 356 mm long, whenever possible. The thickness of the specimen
must be that of the single or composite material used for the restraint
system, except under the following circumstances:
(a) where the material does not adhere to another material at every
point of contact, it must be tested separately;
(b) where the material adheres to another material at every point
of contact, it must be tested as a composite with the other material;
(c) if the thickness of the material exceeds 13 mm, the specimen
must be cut down to that thickness, as measured from the inner surface
of the specimen (see Figure 7);
(d) where a flat specimen cannot be obtained because of surface curvature,
it must be cut to 13 mm or less in thickness; and
(e) the maximum available length and width of a specimen must be used
where either dimension is less than 356 mm and 102 mm, respectively.
|

Figure 7 Thickness of the
Test Specimen
| 7.2.4 The material for the specimen must be cut in
the direction that will produce the most adverse test results, and it must
be positioned so that the inner surface faces downward on the test frame.
7.2.5 Prior to testing, napped or tufted material must be placed
on a flat surface and combed twice against the nap with a comb that has
seven or eight smooth, rounded teeth per 25 mm.
7.3 Test Procedure
7.3.1 Subject to subsection 7.3.2, the specimen
must be mounted so that both sides and one end are anchored between the
U-shaped frames and the free end is even with the edge of the specimen
holder.
7.3.2 Where the specimen is less than 51 mm
wide and cannot be mounted properly in the specimen holder, the specimen
must be placed on wire supports, as specified in subsection
7.1.3, with one side anchored in the short end of the U-shaped frames.
7.3.3 The mounted specimen must be placed in a horizontal position
in the centre of the cabinet.
7.3.4 With the flame adjusted as specified in subsection
7.2.2, the bunsen burner must be positioned with the tip of the flame
19 mm below the centre of the free end of the specimen.
7.3.5 The specimen must be exposed to the flame for 15 seconds.
7.3.6 For the purpose of calculating the burn rate below, the
timing must begin only once the flame from the burning specimen has progressed
a distance of 38 mm.
7.3.7 The time it takes for the flame to travel to a point 38 mm
from the clamped end of the specimen must be measured. If the flame goes
out before reaching the specified point, the timing must stop when the
flame goes out.
7.3.8 The burn rate must be calculated using the following formula:
where:
| B = Burn rate in mm per minute,
D = Distance the flame travels in mm, and
T = Time in seconds for the flame to travel D mm.
|
7.3.9 The requirement contained in subsection
11(1) of Schedule 6 to the RSSRs, which concerns the transmission
of a flame front across the surface of a restraint system, does not apply
to this flammability test.
|
8.
| Webbing Test Procedures for All Restraint Systems
8.1 Measurement of the Width of the
Webbing
8.1.1 Before being measured, the seat
belt and tether strap webbing of the restraint system must be conditioned
for at least 24 hours at a temperature of 23°C ± 2°C
and a relative humidity of between 48% and 67%.
8.1.2 During the measurement of its width, the tension at every
point along the webbing must be no more than 22 N.
8.1.3 The width measurements must be made using properly calibrated
calipers with sufficient adjustment.
8.2 Breaking Strength
8.2.1 The webbing of the seat belt and tether strap must be conditioned
as specified in subsection 8.1.1.
8.2.2 The breaking strength of the webbing
must be measured using a testing machine of suitable capacity verified
as having an error of no more than 1% in the range of the breaking strength.
The webbing must be tested in accordance with ASTM Standard Practices
for Force Verification of Testing Machines, Designation No. E 4-96.
8.2.3 The testing machine must be equipped
with split drum grips, as illustrated in Figure 8,
having a diameter of between 50 mm and 100 mm. The rate of grip
separation must be between 50 and 100 mm per minute. The distance
between the centres of the grips at the start of the test must be between
100 mm and 250 mm. After placing the test specimen in the grips,
the webbing must be stretched continuously at a uniform rate to failure.
8.2.4 The value obtained for the breaking strength of the webbing
must be used for determining the retained breaking strength, as required
by subsections 8.4 , 8.5, and 8.6.
|
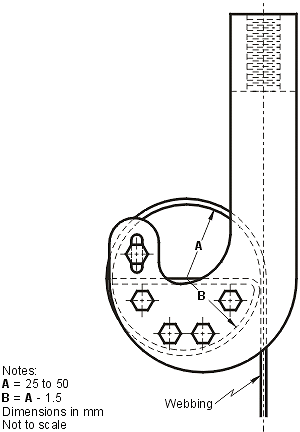
Figure 8 Split Drum Grips to be used in the Webbing Breaking Strength Tests
| 8.3 Elongation
8.3.1 Elongation must be measured during the breaking strength
test specified in subsection 8.2 using the following
procedure:
(a) A preload of between 196 N and 245 N must be
placed on the webbing mounted in the grips of the testing machine, and
the needle points of an extensometer, in which the points remain parallel
during testing, must be inserted into the centre of the specimen. Initially,
the points must be set between 100 mm and 200 mm apart, and
(b) When the force on the webbing reaches the applicable value
specified in paragraph
9(g) of Schedule 6 to the RSSRs, the increase in separation of the
points of the extensometer must be measured and the percent elongation
must be calculated to the nearest 0.5%.
8.4 Resistance to Abrasion
8.4.1 The webbing of the restraint system must be tested for
resistance to abrasion by rubbing a test specimen over a hexagonal rod,
as illustrated in Figure 9.
|

Figure 9 Hexagonal Rod used for the Abrasion Test
| 8.4.2 One end of the webbing (A) must be attached
to the weight (B), which must have a mass of either:
(a) 2.35 kg ± 0.05 kg for the webbing
of a restraint system for which the maximum recommended mass of the
occupant is 22 kg or more, or
(b) 1.50 kg ± 0.05 kg where the
maximum recommended mass of the occupant is less than 22 kg.
8.4.3 The webbing must be passed over two unused abrading edges
of the hexagonal rod (C) and the other end attached to an oscillating
drum (D) that has a stroke of 330 mm. Guides must be used to prevent
the webbing from moving along the axis of the hexagonal rod. The drum
must be oscillated for 5 000 strokes or 2 500 cycles, at a rate
of 60 ± 2 strokes per minute or 30 ± 1 cycles
per minute.
8.4.4 The abraded webbing must be conditioned as specified in
subsection 8.1.1 and tested for breaking strength
in accordance with the procedure specified in subsections 8.2.2
and 8.2.3.
8.4.5 The percentage of the retained breaking strength for the
abraded webbing (RBS) must be calculated as follows:
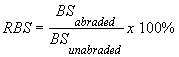
where:
|
| =
| is the breaking strength
value
of the abraded webbing, and
|
BSunabraded
| =
| is the breaking strength
value of the unabraded webbing obtained in accordance with the requirements
of subsection 8.2
|
|
| 8.5 Resistance to Light
8.5.1 A strip of webbing at least 500 mm in length must
be suspended vertically on the inside of the specimen rack in a Type E
carbon-arc light-exposure apparatus as specified in ASTM Standard Practice
for Operating Light-Exposure Apparatus (Carbon-Arc Type) With and Without
Water for Exposure of Nonmetallic Materials, Designation No. G 23-96,
except that the filter used for 100% polyester yarns must be chemically
strengthened by soda-lime glass with a transmittance of less than 5%,
for wave lengths less than or equal to 305 nm, or with a transmittance
of 90% or more, for wave lengths from 375 nm to 800 nm.
8.5.2 The light exposure apparatus must be operated without water
spray at an air temperature of 60°C ± 2°C, as
measured at a point 25 mm ± 5 mm outside the specimen
rack and midway in height. The temperature sensing element must be shielded
from radiation.
8.5.3 The test specimen must be exposed to the light from the
carbon arc for 100 hours and then conditioned as specified in subsection
8.1.1.
8.5.4 The colourfastness of the exposed and conditioned specimen
must be determined using Evaluation Procedure 1, Gray Scale for Color
Change, published by the American Association of Textile Chemists
and Colorists (AATCC). The breaking strength of the specimen must be determined
using the procedure specified in subsections 8.2.2 and 8.2.3.
8.5.5 The percentage of the retained breaking strength for the
exposed webbing (RBS) must be calculated as follows:
where:
|
| =
| is the breaking strength
value
of the exposed webbing, and
|
BSunexposed
| =
| is the breaking strength
value of the unexposed webbing obtained in accordance with the requirements
of subsection 8.2
|
|
| 8.6 Resistance to Micro-Organisms
8.6.1 A strip of webbing at least 500 mm in length must
be preconditioned in accordance with the requirements of Appendices A(1)
and (2) of AATCC Test Method 30-1993, Antifungal Activity, Assessment
on Textile Materials: Mildew and Rot Resistance of Textile Materials,
and then subject to Test I, "Soil Burial", of that test method.
8.6.2 The breaking strength of the tested specimen must be determined
by the procedure specified in subsections 8.2.2
and 8.2.3.
8.6.3 The percentage of the retained breaking strength for the
exposed webbing (RBS) must be calculated as follows:
where:
|
| =
| is the breaking strength
value
of the exposed webbing, and
|
BSunexposed
| =
| is the breaking strength
value of the unexposed webbing obtained in accordance with the requirements
of subsection 8.2
|
|
| 8.7 Colourfastness
to Staining
8.7.1 The webbing must be tested for colourfastness to staining
using the procedure specified in AATCC Test Method 107–1991, Colorfastness
to Water, except that the following must be used in the testing:
(1) distilled water,
(2) the AATCC perspiration tester,
(3) a drying time of four hours for section 8.4 of the AATCC test
method, and
(4) section 9 of the above AATCC test method when determining the
colourfastness to staining based on the AATCC Chromatic Transference
Scale.
8.8 Colourfastness to Crocking
8.8.1 The webbing must be tested using the procedure specified
in AATCC Test Method 8-1996, Colorfastness to Crocking: AATCC Crockmeter
Method.
|
9.
| Seat Belt Assembly Hardware Test for All Restraint
Systems
9.1
Conditioning Procedure
During conditioning, the buckles must be unlatched, and the same conditioned
hardware parts must be used for the tests specified in subsections
8(3) and 8(4) of Schedule 6 to the RSSRs.
9.2 Corrosion Resistance
9.2.1 The seat belt assembly must be tested using ASTM Standard
Practice for Operating Salt Spray (Fog) Testing Apparatus, Designation
No. B 117-95. Any temporary surface coating or material must be removed
from the specimen before testing. The test period for all hardware must
be 25 hours in duration and consist of one 24-hour period of exposure
to salt spray, followed by 1 hour of drying time.
9.2.2 The seat belt assembly must be positioned in the salt spray
test chamber in such a way that corrosion is most likely to develop on
the larger surfaces. At the end of the test, the seat belt assembly must
be washed thoroughly with water to remove the salt.
9.2.3 After drying the test specimen for at least 24 hours under
the laboratory conditions specified in subsection
8.1.1 of this test method, the attachment hardware must be examined
for ferrous corrosion on all the surfaces that can be contacted by a sphere
19 mm in diameter. The other hardware must be examined for any ferrous
or non-ferrous corrosion that could be transferred, either directly or
by means of the webbing, to an occupant or to an occupant's clothing by
the seat belt assembly.
9.3 Temperature Resistance
A seat belt assembly with plastic or non-metallic hardware must be tested
in accordance with the conditions specified in Procedure D of ASTM Standard
Practice for Determination of Weight and Shape Changes of Plastics Under
Accelerated Service Conditions, Designation No. D 756-93. The
dimension and weight measurements are not required.
|
|